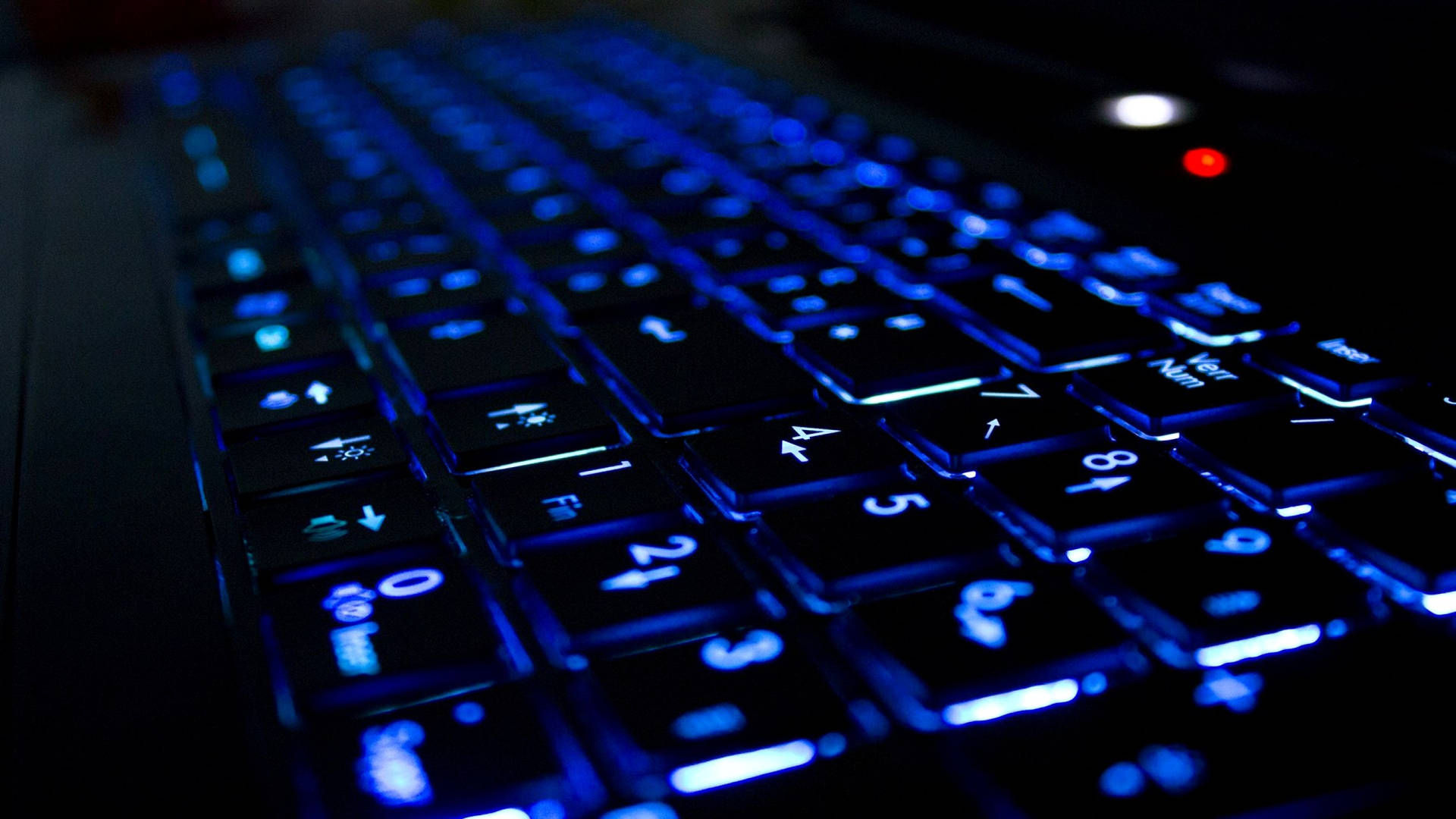



Services
Root Cause Analysis (RCA) encourages us to look beyond the obvious symptoms to identify the underlying causes of a problem.
By addressing the root cause directly, organizations can effectively disrupt recurring issues and foster long-term solutions.
This proactive approach not only enhances operational efficiency but cultivates a culture of continuous improvement within the organization
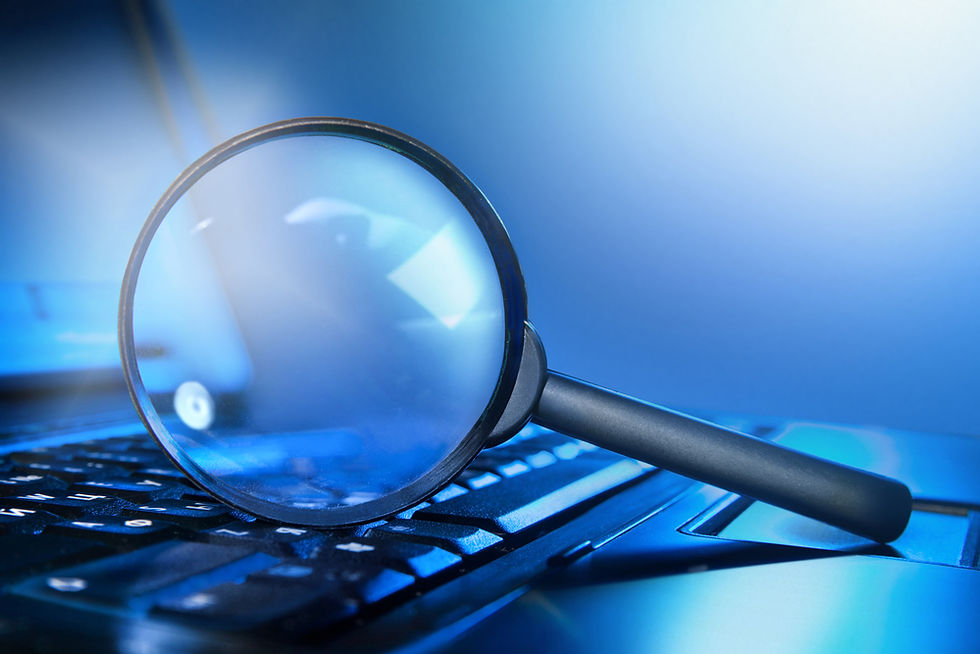
Root Cause Process
​
Root Cause Analysis is a systematic iterative process that identify the fundamental reasons behind an event which involves Key Steps:
​
1. Define the Problem
Describe what’s going wrong and specify what happened, where and when.
​
2. Collect Information
Gather all the facts about the problem. Talk to people involved, look at records, and note any patterns.
​
3. Look for Causes
Brainstorm possible reasons why the problem happened. Use RCA tools like asking “Why” several times to dig deeper.
​
4. Find the Main Cause (Root Cause)
Keep asking questions until you find the real reason behind the problem, not just the obvious one.
​
5. Fix the Root Cause
Come up with a solution(s) that addresses the root cause(s). Make changes so the problem doesn’t happen again.
​
6. Check if it Worked
Watch what happens after the fix. Make sure the problem is truly solved and doesn’t reappear.
This process helps you solve problems for good, not just cover them up.
​
Our Methods
-
Event Causal Factor Charting
-
5 Whys
-
Barrier, Change and Task Analysis
-
Fishbone Analysis
-
Fault Tree Analysis
​
​
Service Options
Simple Issues - A simple organization issue is a problem that is limited in scope, involves a few variables, and has a clear direct cause and affect relationship. These issues often involve a single process or department and can usually be resolved using straight forward root cause analysis methods such as the 5 Whys technique.
​
Complex Issues- A complex organization issue is characterized by multiple, interrelated factors spanning across various processes, departments, or systems. These problems often involve several layers of contributing causes, including organizational, human, and physical factors, and may not have a single root cause. Addressing complex issues requires more advanced analysis tools such as the Fishbone diagram to map out the interactions and dependencies that led to the problem. An example would be recurring quality failures in a product line caused by a combination of training gaps, process inefficiencies, and supplier inconsistencies.
​
Option 1
Quick Event Investigation- Simple Issues
Timeframe- 1-2 weeks
​
Option 2
Full Root Cause Analysis Investigation
Timeframe – 1 to 2 months.